The most underrated material in the modern world
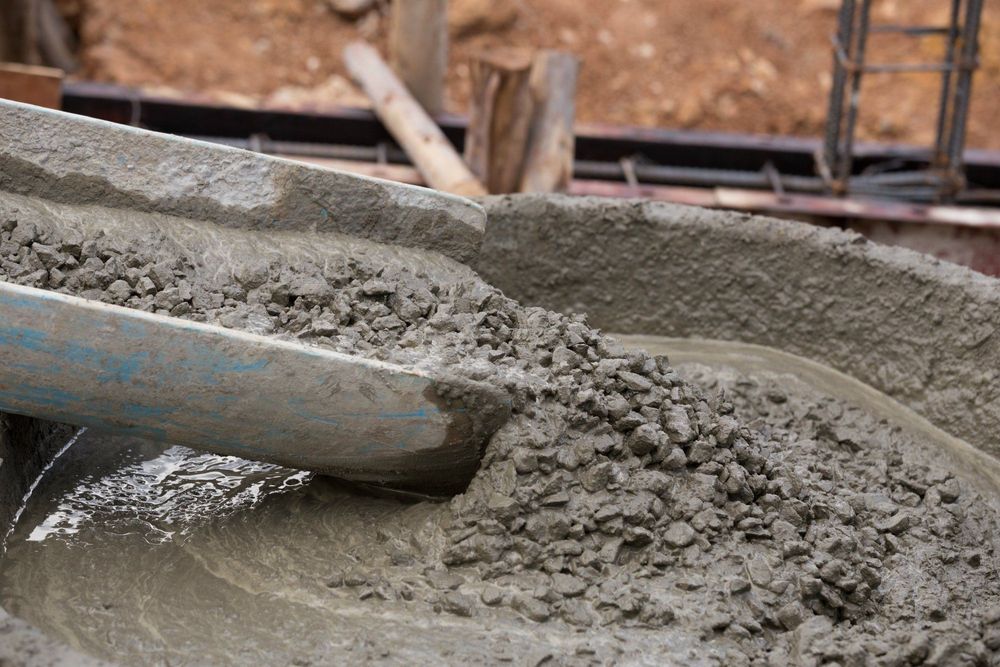
Concrete. A blot on the urban landscape, right? Boring, ugly, lifeless and destructive, right?
Well hold on. Because here are a few reasons why concrete is actually surprising, dynamic & incredibly complex. And not just that: it is one of the most overlooked cogs in the modern machinery of civilisation. This goes both ways: it’s overlooked in good ways (we tend to ignore how amazing it is - but no harm done there) and also bad ways (we tend to overlook how central concrete is to resolving climate change).
Perhaps the main thing you’ll be aware of when it comes to concrete is its sheer scale. Every minute each day construction firms around the world pour out the equivalent of more than 200,000 bathtubs of concrete. Every minute!
Every year we pour enough concrete to cover the entire landmass of England.
The vast majority of it these days is being poured in China, to build bridges, skyscrapers, high speed rail etc. Indeed China produced more cement in the past three years alone (2018-2020) than the US did cumulatively in EVERY year since the first Portland cement plant opened in 1865.
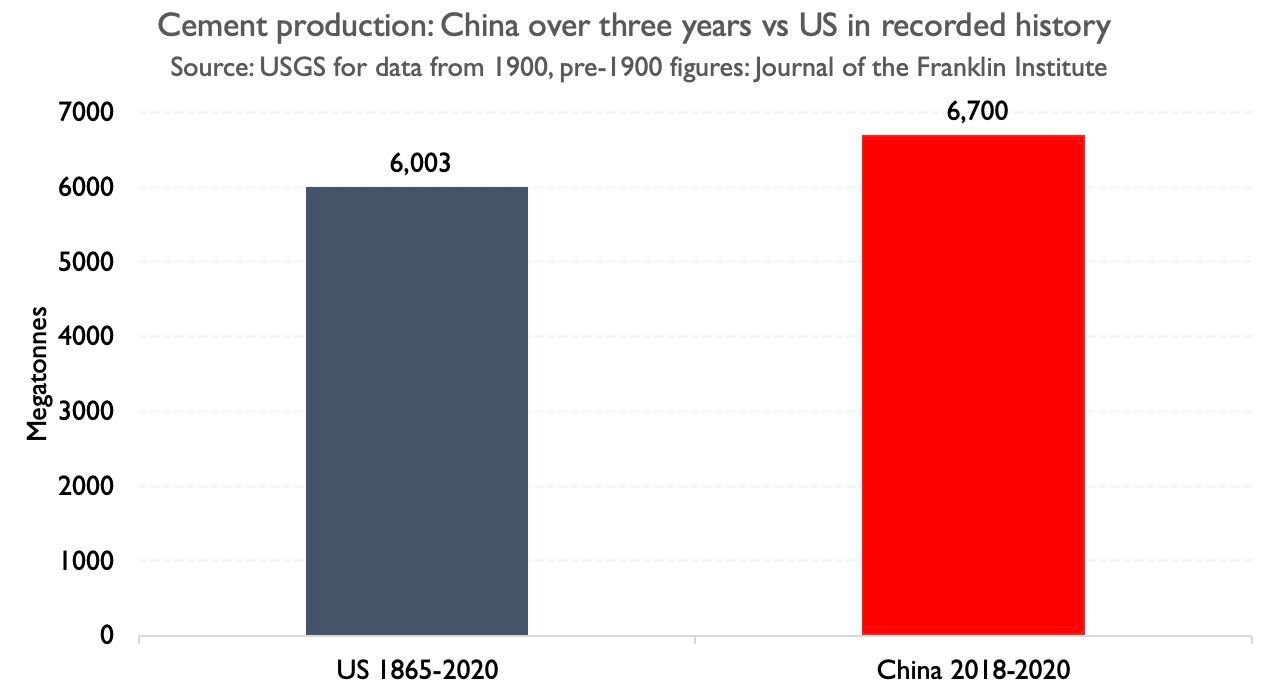
Or here’s another way of looking at it. The bars below represent the total amount of cement produced over the past decade in the US (dark blue) and in China (red). You get the idea. These are staggering sums.
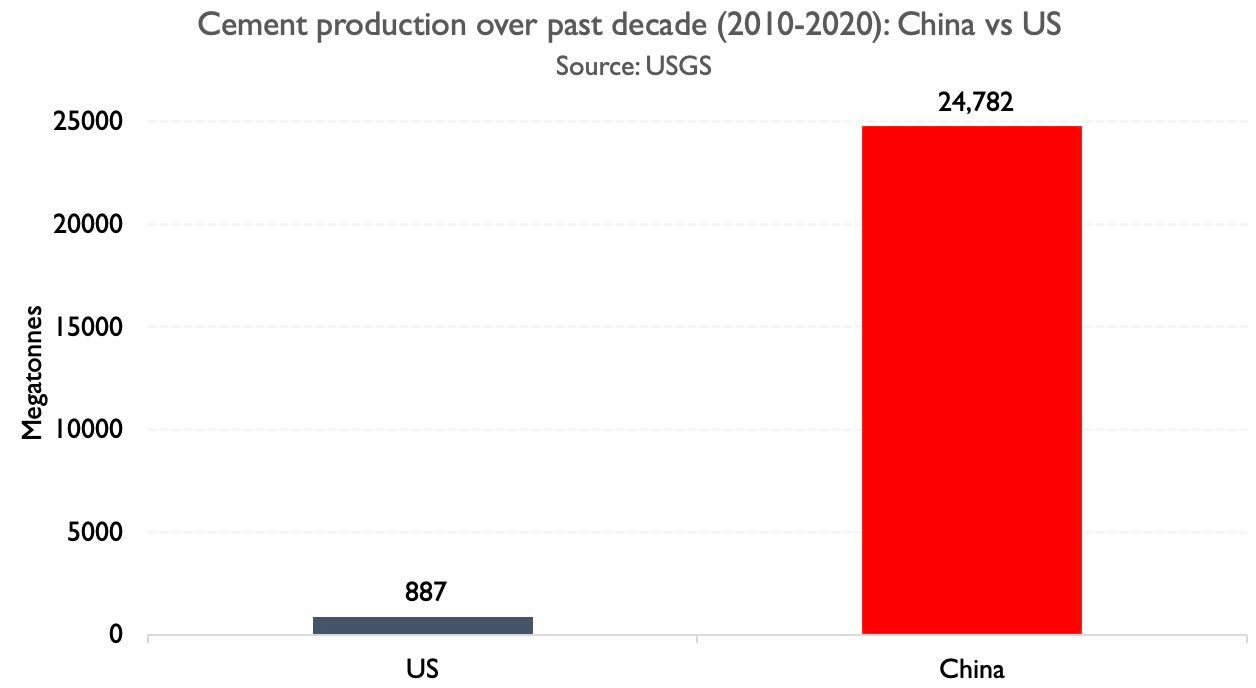
Anyway, at this stage perhaps you’re wondering why I'm saying both "cement" and "concrete". Actually they’re slightly different things. Cement is the magic ingredient inside concrete. Concrete is basically sand plus gravel plus cement. Add water and you get an extraordinary reaction.
Calling it extraordinary isn't overdoing it. The cement reacts with the water to create a kind of gel which quickly and then slowly begins to cure into stone. Look under a microscope and you see lots of tiny stony tendrils forming which bond to each other and the sand/stone.
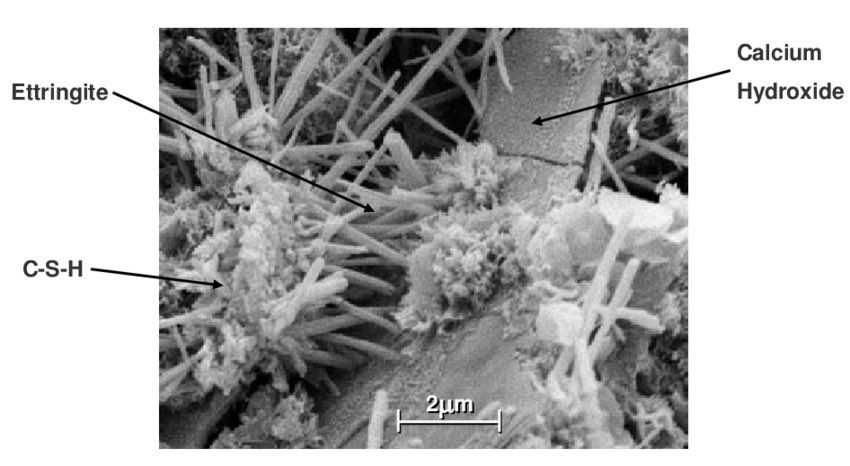
Scientists still don't 100% understand what's going on inside cement when it's setting. In chemistry labs this remains hotly-debated territory. Also intriguingly, it keeps on curing long after it's apparently set. The Hoover dam is still curing nearly a century after being built!
But the upshot of the chemical reaction is to create a kind of stone you can pour into a mould. It’s hard these days to imagine how revolutionary this was back in the 19th century when the main alternative was bricks or masonry - which was very labour intensive and considerably less strong.
Concrete, on the other hand, is very, very strong, especially when you combine it with steel reinforcement bars (rebar) which also give it tensile strength (so you can build bridges with it). The 20th and 21st century world is literally built on concrete, mostly reinforced concrete.
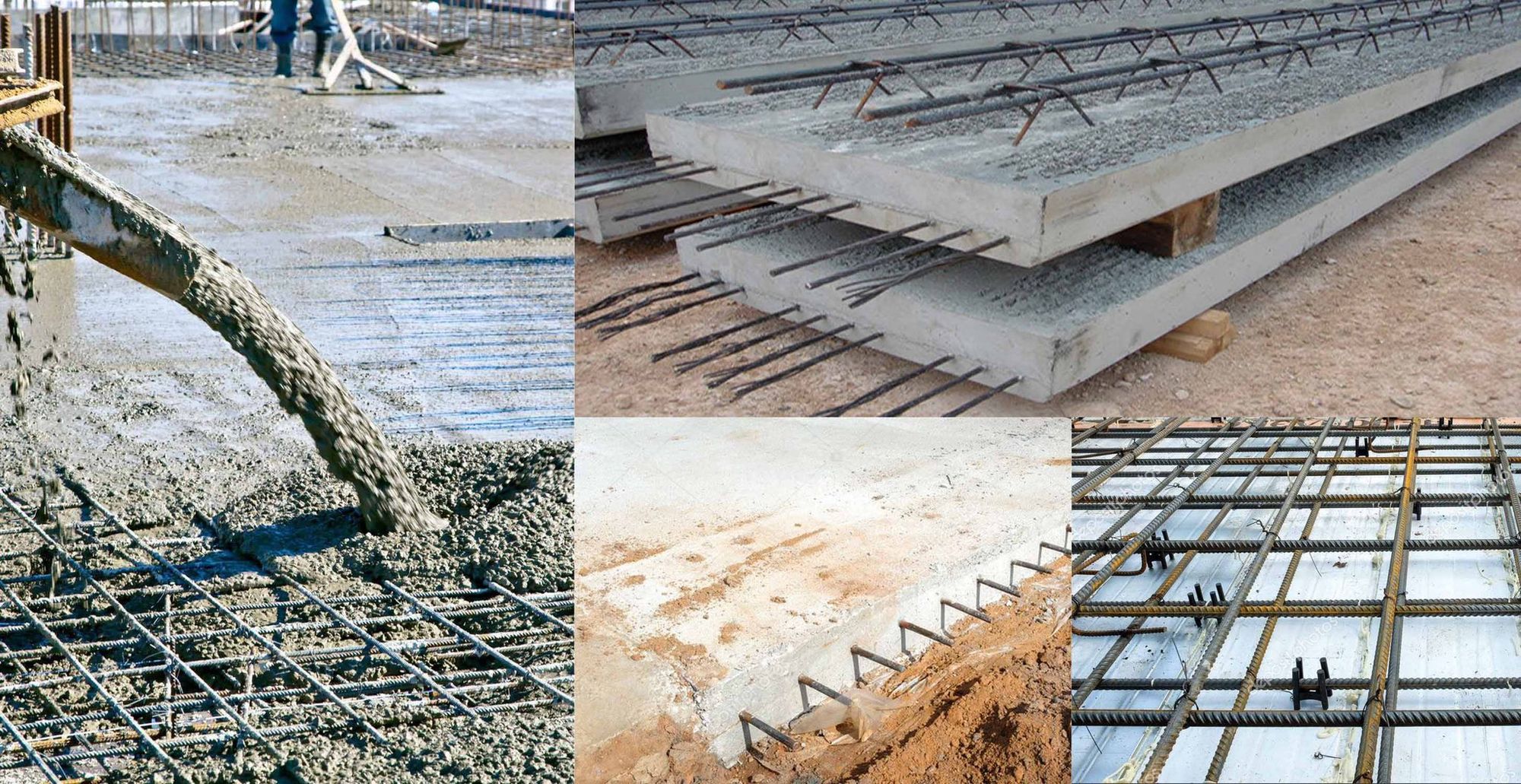
Now, we are not the first civilisation to be v reliant on concrete. The Romans had their own form of concrete & there's evidence our ancestors used a form of cement as long as 10k yrs ago. The Colosseum is partly built out of concrete, behind the brickwork and in the foundations.
That brings us to the most amazing building in Rome: the Pantheon. An enormous, pristine, beautiful and quite delicate-looking dome, all built out of concrete. Two thousand years ago! It's still the world's biggest unreinforced concrete dome even today.
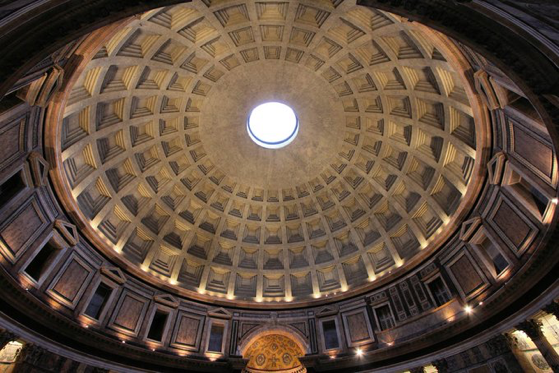
But while modern concrete is stronger than the Roman variety it tends to be less resilient in certain respects. This is usually down to the corrosion of the steel bars inside it. This is an enormous problem these days - perhaps the biggest problem in structural engineering. Much of the money spent on roads in the US and the UK is on repairing decades-old motorway bridges and structures which face concrete rebar corrosion. It’s hard, by the way, to know how widespread an issue this is in the UK, since our authorities are considerably less transparent with the information on this than, for instance, the US. The Times recently got a rare glimpse beneath this veil of secrecy, thanks to a Freedom of Information request.
Anyway, after the fall of the Roman Empire, the recipe for concrete was forgotten. Only in the 15th century, when an old manuscript by Vitruvius resurfaced with hints about the recipe, was interest in this building craft re-ignited. It sparked a race to "re-invent" concrete anew. It’s funny: when historians write about the enlightenment, the industrial revolution and that great era of invention, they often talk about steel and science and electricity and so on. They tend to overlook concrete & cement. But in the 18th and 19th century many of the world's greatest minds were focused on this challenge.
There were countless contenders making artificial stone but the eventual winner of this race was someone called Joseph Aspdin, who patented Portland cement in 1824 (the "Portland" bit was essentially a branding exercise, since Portland stone from Dorset was v fashionable). No-one is quite sure, by the way, whether Aspdin came up with the recipe himself or nicked it from someone else. If you're interested in this topic and, well, concrete more generally, Concrete Planet by Robert Courland is well worth a read.
Anyway, Portland cement wasn't quite the same as the Roman variety, whose secret ingredient was a kind of volcanic ash called Pozzolana. In most ways it's actually stronger. Though in terms of water resistance we are still learning much from the Roman variety.
To simplify enormously, Portland cement is a powder formed when you roast limestone/chalk with clay, sand and, occasionally, other additives such as iron oxide. You end up with black, unpromising-looking nodules, which are called clinker. Crush them and you have a basic cement.
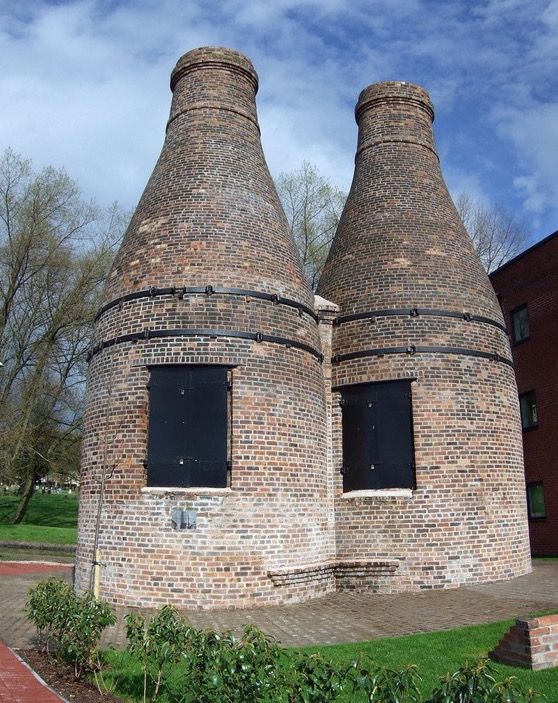
This all happens in a kiln. Back in the day these were "bottle kilns": like those old pottery kilns you see in Stoke-on-Trent and elsewhere. But these days they are rotary kilns, vast, hot, titled tubular ovens through which the ingredients tumble as the chemical reaction occurs.
I went to the cement plant in Rugby the other day. It was unexpectedly thrilling. The kiln is the enormous tube here (not that tall tower where the chimney is, whose main function is to pre-heat the ingredients).
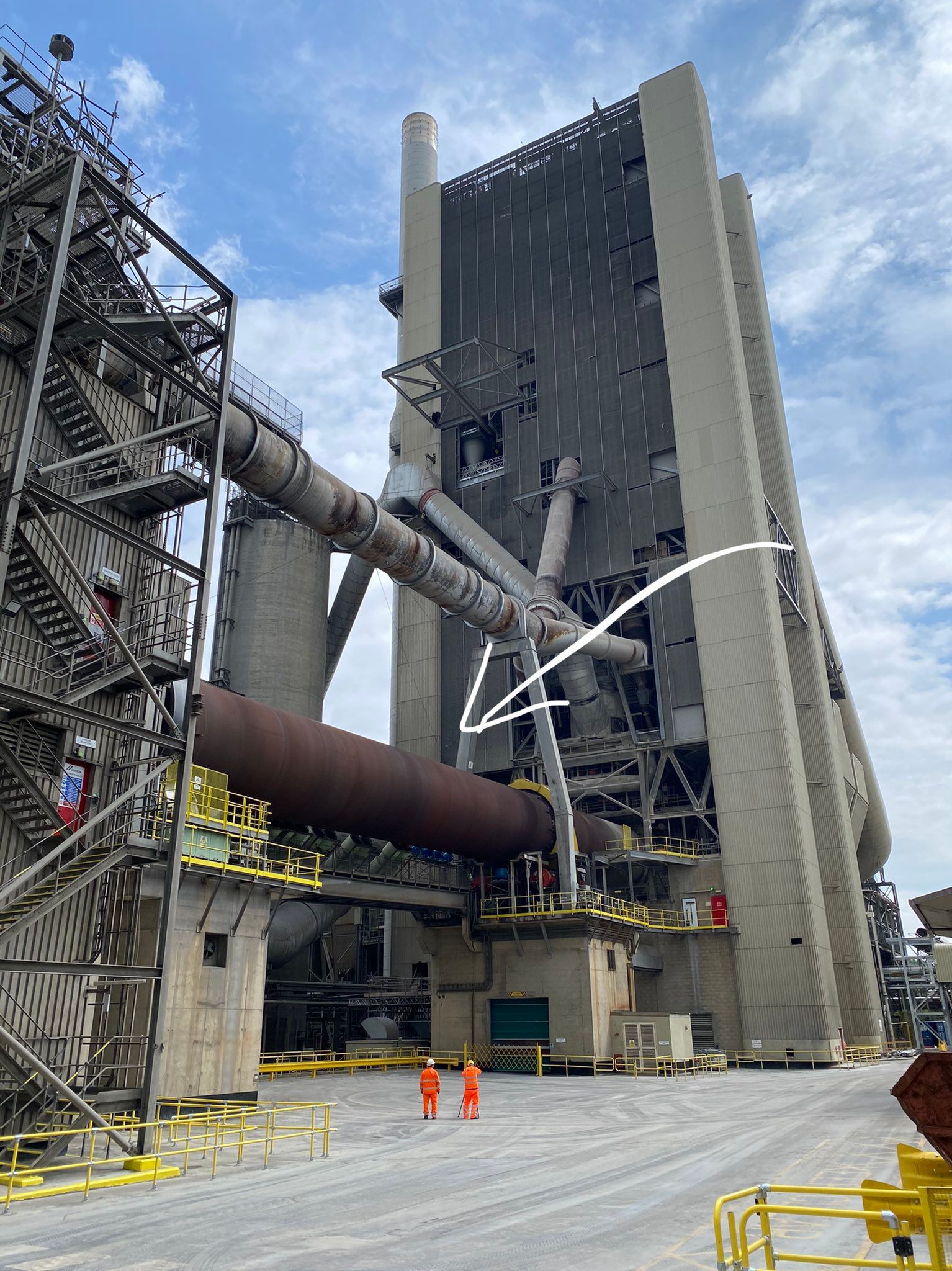
The kiln here is the biggest in the UK. This plant is actually the oldest still operating in the UK - possibly the world. This plant was making cement for the Victorian industrial revolution - cement during WWI and WWII - cement today for HS2 and more. This is a mainstay of Britain’s economy. Not that anyone talks about it much.
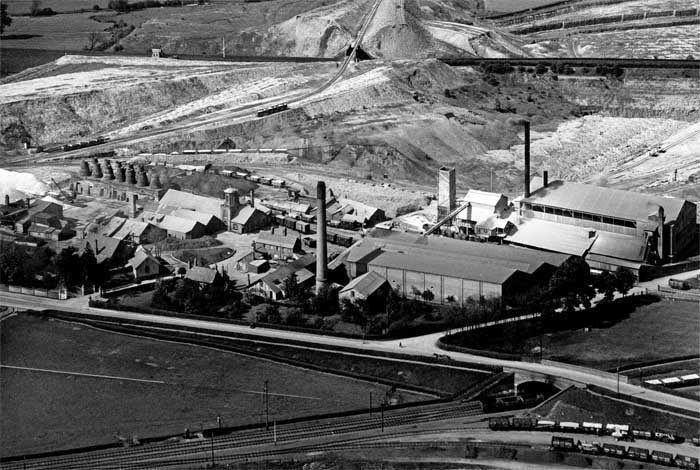
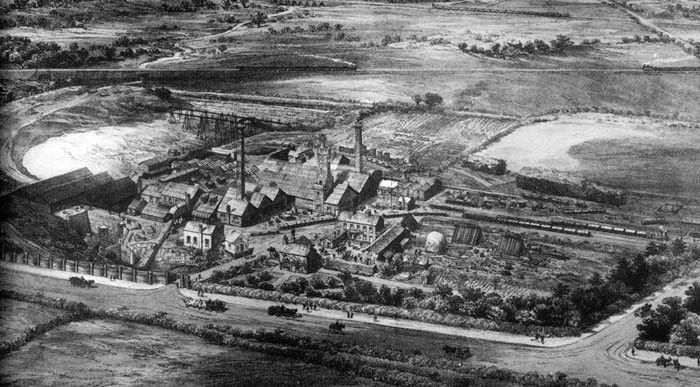
The rotary kiln has to keep turning, 24 hours a day, partly because of all the demand for cement (there has been a LOT of demand for cement post Covid - home renovations, building work etc) but even more importantly because if it stopped moving the tremendous heat inside would melt the walls and it would sag and fail. This would be very bad, the plant manager said, with some understatement.
Cement plants like these don't get much attention. Most manufacturing stories these days fixate on car plants and steelworks but cement production is a crucial part of the UK economy, because of how many sectors it underpins (construction, property, transport). And unlike most sectors we are nearly self-sufficient in cement.
But there's growing focus on these kilns these days, because cement production happens to be one of the trickiest obstacles in getting carbon emissions down to net zero by 2050. Cement manufacture is responsible for roughly 7% of global emissions. More than aviation and deforestation combined. It's a BIG deal.
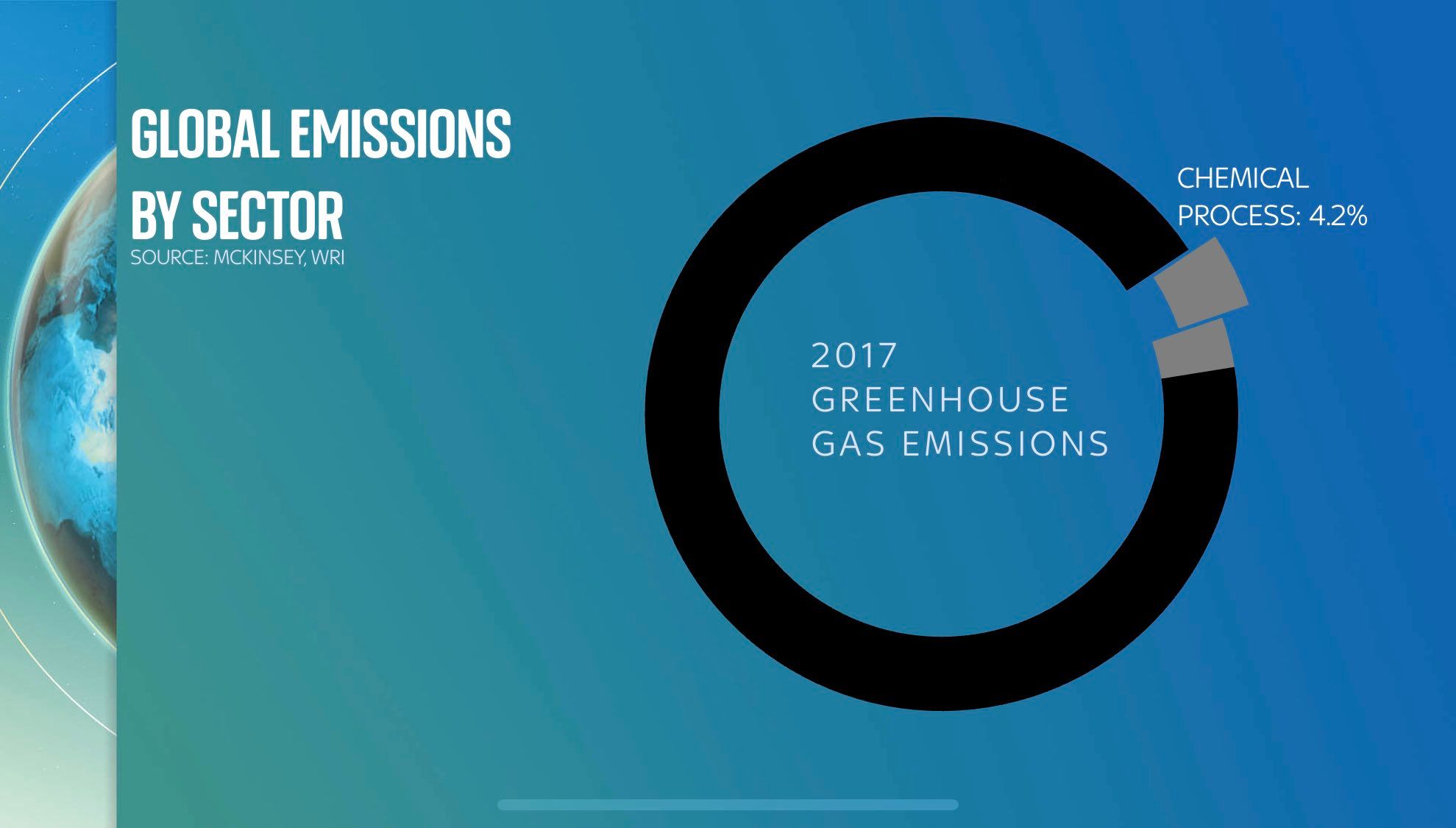
Actually it's worth being a bit more granular about this. Because that 7% actually comprises two parts: the chemical reaction as calcium carbonate (chalk/limestone) is heated and the carbon bonds with oxygen, creating calcium oxide (quicklime, a key component of cement) and co2. Then there's the emissions from the heat source for the kiln, traditionally coal.
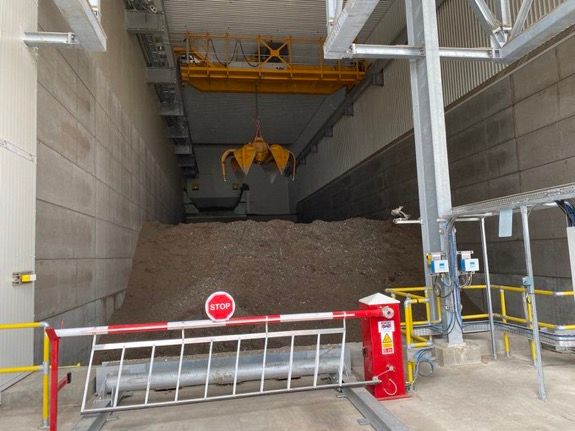
Now it's relatively straightforward (emphasis on relatively) to remove coal from the equation. The Rugby plant (run by Cemex these days) now uses something called Climafuel - essentially processed waste - to heat its kilns. You can see the big hangar here where they store it. It's a bit smelly. But quite effective and far greener than what used to go into the kiln.
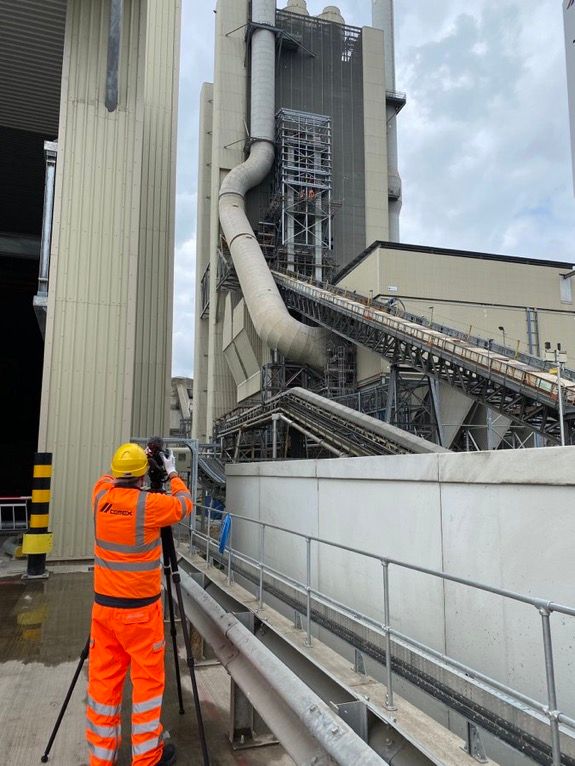
You can barely see anything coming out of the chimney here these days. Most of the other pollutants - Sox and Nox - are filtered out. This plant - and the UK cement industry - is far far greener than in previous years. In this country cement CO2 emissions are down 53% since 1990 - partly by reducing energy emissions, partly by adding things to the final mix. But the CO2 from that chemical reaction is a far tougher nut to crack.
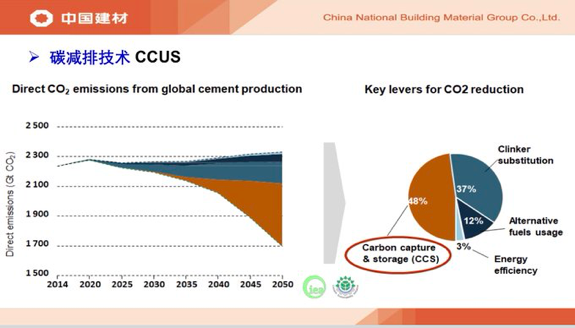
You can't make Portland cement - you can't achieve the chemical reaction in the kiln - without carbon emissions. So for the cement industry the only foreseeable way to get to zero emissions is via carbon capture & storage. The problem with CCS is it's very expensive and while the tech works in theory we've yet to see it applied at scale. Those are big challenges. Some would say insurmountable.
Which raises another question: can we make cement without emitting co2 at all? Well, yes and no. One alternative is alkali-activated cements where you add an alkali solution to blast furnace slag or coal fly ash or waste incinerator ash or metakaolin. You get a really strong cement without co2 emissions from the reaction. A few weeks ago Brant Walkley and his team at Sheffield Uni mixed up some samples. On the left is traditional Portland cement. On the right is one that is zero carbon!
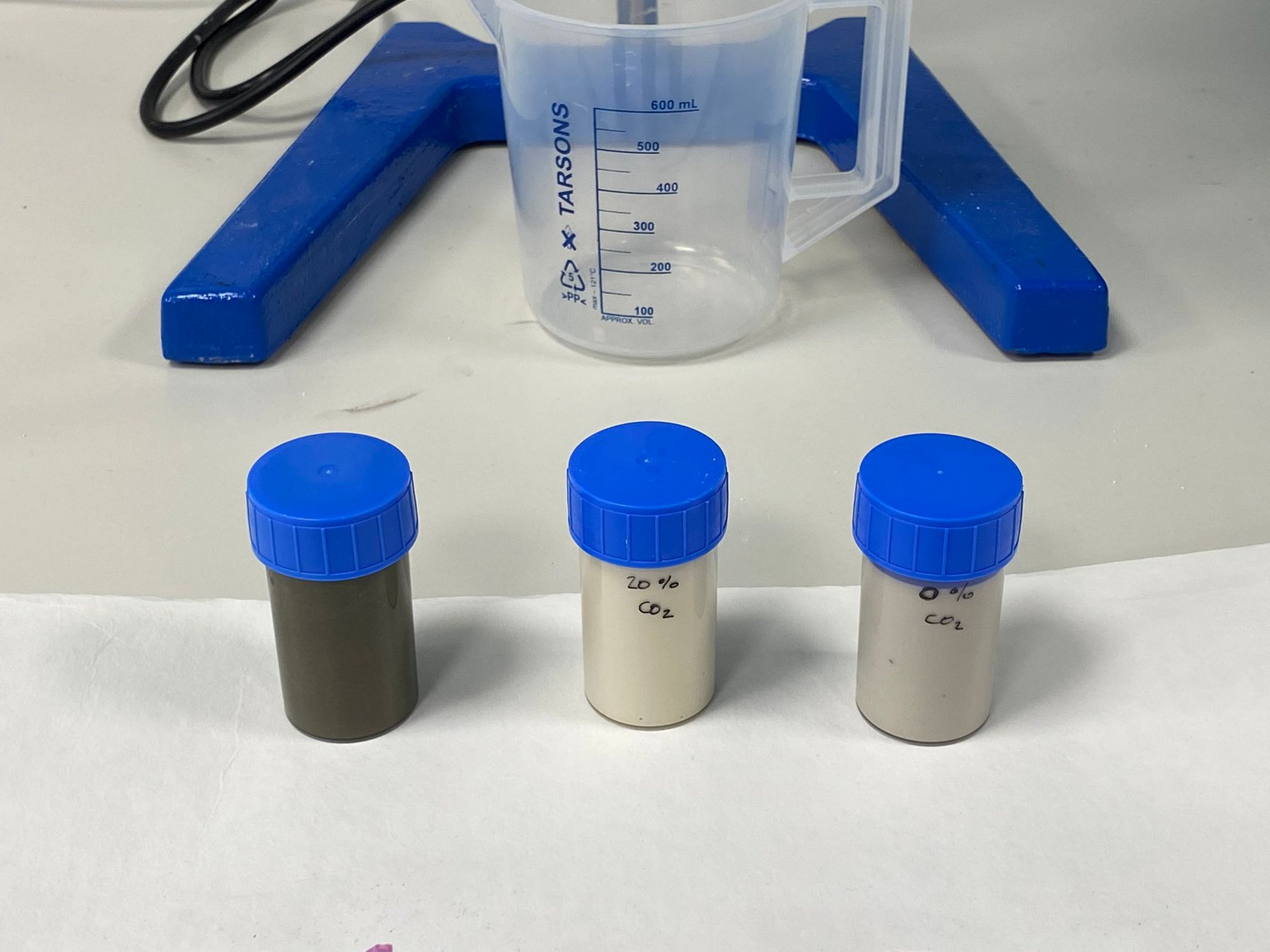
By the way one of the other benefits of this alkali-activated cement is that it is more resilient to the kinds of corrosion problems you get in traditional reinforced concrete. Why? Because it has a higher pH than traditional Portland cement, which helps protect steel from rust. These blocks are alkali-activated (the "zero carbon" is on the right). They've been sprayed with a solution which goes pink when there's a high pH.
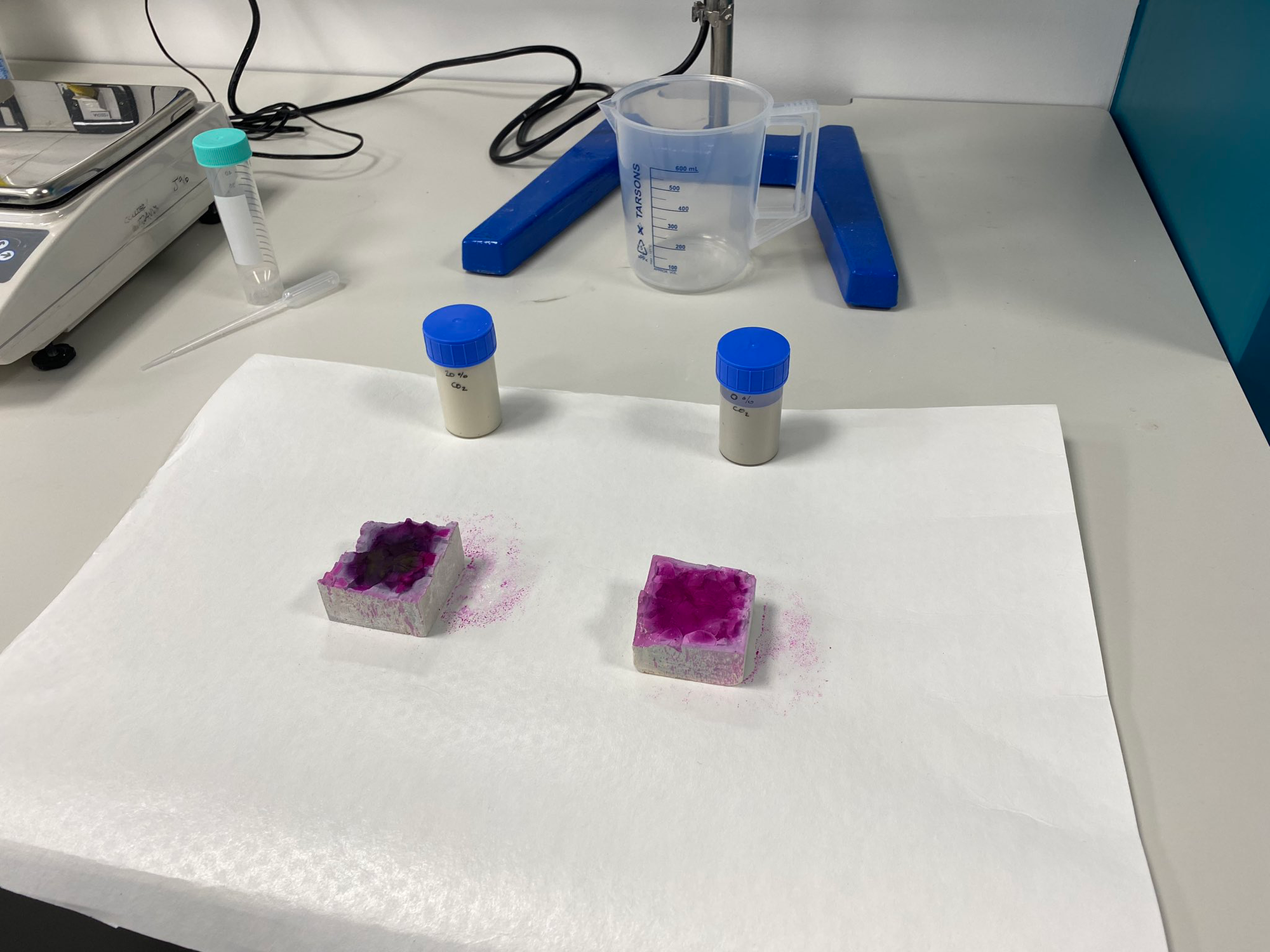
The remaining question is how well these cements stand up to real world use/abuse over decades. We have 200yrs of playing around with Portland cement but much less experience with these ones. Tho there are one or two structures around the world made with alkali-activated cement - esp, surprising as this might sound, in the ex-Soviet Union.
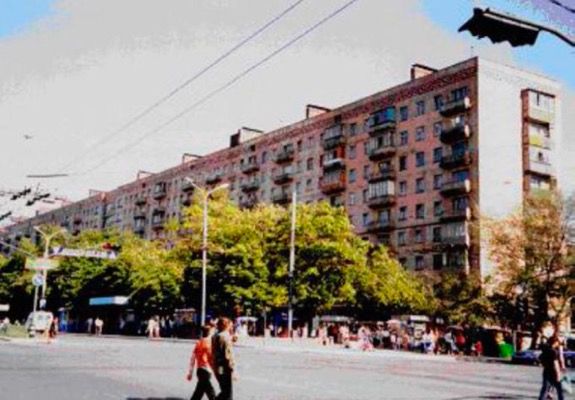
Faced with shortages of Portland cement in the Soviet era, some chemists/builders experimented with these unconventional cements. Above is an apartment in Mariupol, Ukraine. Though I doubt many of its residents realise it, this building is a site of enormous interest to scientists these days.

There's also an old jetty at Skinningrove in North Yorkshire which was also built with cement made with blast furnace slag, long before the Soviet efforts. Only problem? It got renovated recently and I suspect (though am yet to have this confirmed) that the renovation used Portland cement - albeit with some added blast furnace slag or fly ash - as is often the case with modern cements. Not, however, the unique mix with which it was first made.
Anyway, while these kinds of cements are much better from a carbon emissions perspective the problem is they're quite hard to scale up. And the defining feature of concrete is scale (back to those first few tweets). And ease of use. One of the most amazing things about concrete is that pretty much anyone can make it.
Anyway, we're left with a simple quandary. If we are going to continue relying on cement (and it's hard to imagine 21st century civilisation without it) then we need to make some big technological leaps - and soon. Lots of money going into batteries/hydrogen/solar etc. But this issue, unsexy as it might be, is just as important.
If you're still, god forbid, interested in cement and concrete after all that, here's a short Sky News film I made with about it. I originally wrote up the above as a blog post but never ended up posting it (I’m just getting around to that now). I did however turn it into a Twitter thread which you can read here:
What’s the most underrated material in the modern world?
— Ed Conway (@EdConwaySky) August 16, 2021
How about CONCRETE?
Often dismissed as boring, ugly & inert.
Concrete is actually surprising, dynamic & incredibly complex.
With that in mind here are a few reasons why we need to start talking about concrete 🪨
🧵 pic.twitter.com/sEPSdW4zGh
Comments ()